ARNOTT TIPS FOR MAINTAINING AND REPAIRING AIR SUSPENSION SYSTEMS
The experts at Arnott wish to share the following six tips for working on air suspension
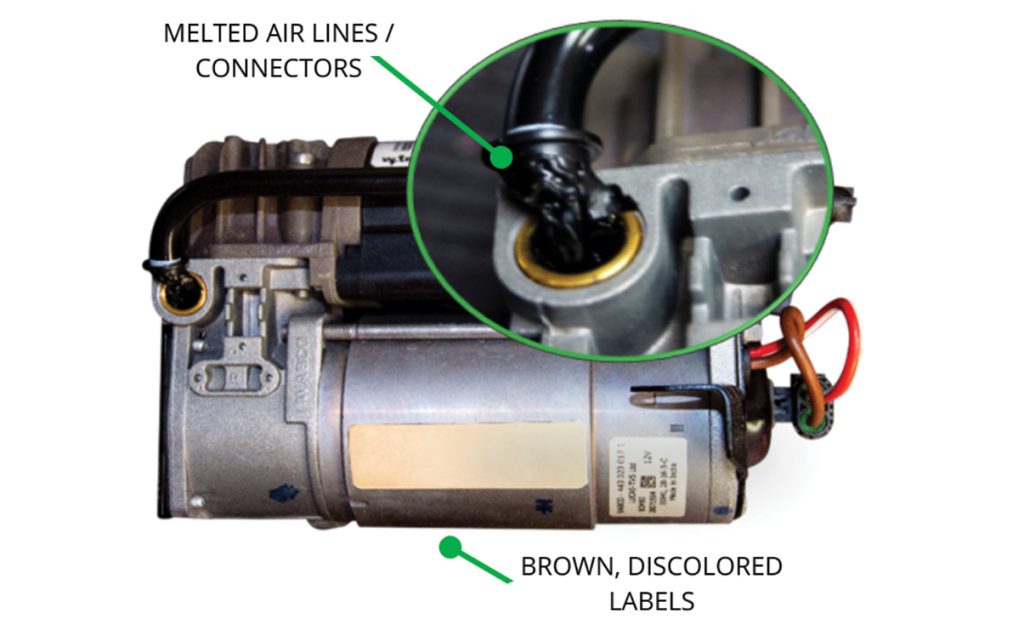
Arnott Suspension Products explains that air suspension systems offer superior comfort and handling, but proper maintenance and repair are essential to ensure they function optimally.
Here, the company provides six essential tips for maintaining, diagnosing, and repairing your vehicle’s air suspension system.
- Prioritise safety
Air suspension systems can operate at high pressures, so ensure the system is depressurised and power is disconnected.
Prevent contamination by keeping grease and dirt away. Always wear proper protective gear and securely lift the vehicle. Safety measures protect both the technician and the system. - Depressurise properly
Controlled depressurisation prevents damage. Never remove fittings abruptly – some vehicles require diagnostic tools to open solenoids to release air.
If available, activate “jack mode” to stop the system from adjusting when the vehicle is lifted. - Avoid common installation errors
Improper handling can lead to system failure. Always support the vehicle when the system is depressurised and never pressurise air springs during installation, as both can cause improper unfolding and crimp ring damage.
Lowering a vehicle without pressurisation can overwork and overheat the compressor and possibly damage the compressor relay.
Follow torque specifications – especially with VOSS connectors. These typically require no tightening, and overtightening can cause leaks or thread damage.
Arnott recommends using a torque wrench when needed. - Detect early signs of failure
Catching failing parts early saves time and money. Signs of a failing compressor include melted lines, discoloration, or a burnt smell – often due to leaks causing overuse.
A drop in ride height overnight suggests a leak; use soapy water to find it. Uneven height may point to a faulty valve block as well.
Inspect struts for oil leaks. Oil can degrade air sleeves and reduce lifespan, while internal damper leaks hinder performance, overburdening the air spring. - Address root causes, not just symptoms
Replacing a failed part without resolving the underlying issue may lead to repeat failures.
For instance, a leaking shock might damage an air spring, which in turn stresses the compressor.
Always replace relays with compressors to prevent premature failure due to constant running. Once repairs are complete, perform a comprehensive system check. - Diagnostic tools and recalibration
After service, proper calibration is essential to ensure everything works as intended.
Recalibrate ride height sensors with a diagnostic scan tool to verify and adjust ride height settings to avoid faults and ensure correct function.
After test driving the vehicle, confirm that no diagnostic fault codes have reappeared in the system.
For more from Arnott, visit www.arnottinc.com