BOSCH OPENS NEW SEMICONDUCTOR TEST CENTRE
The new testing facility for chips and sensors is located in Malaysia
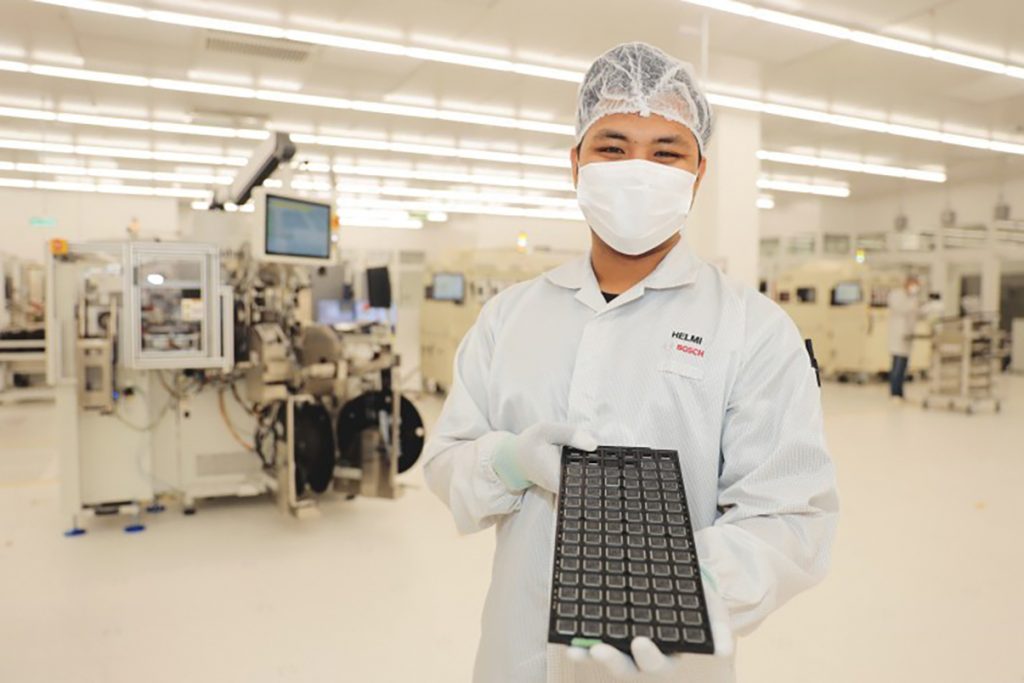
Global demand for chips for the automotive and consumer goods industries remains high, which is why Bosch is continuing to expand its semiconductor business.
The company has now opened a new test centre for chips and sensors in Penang, Malaysia, at a cost of some 65 million euros. It also plans to invest a further 285 million euros at the site by the middle of the next decade.
“With our new semiconductor test centre in Penang, we are creating additional capacity within our worldwide manufacturing network to meet the continued high demand for chips and sensors,” Bosch Board of Management Chairman, Dr Stefan Hartung, said.
“Semiconductors are a decisive success factor for all Bosch business areas, and the expansion of this business is strategically very important.”
In total, Bosch has some 100,000 square meters of land available on Penang’s mainland strip. The new test centre currently covers more than 18,000 square meters and includes clean rooms, office space, and laboratories for quality assurance and manufacturing.
By the middle of the next decade, up to 400 associates will be working there. With the new factory and a total of 4,200 associates, Penang is now Bosch’s biggest location in Southeast Asia.
Semiconductor manufacturing can basically be divided into two sections: frontend manufacturing and backend manufacturing.
For the latter, Malaysia is an important hub in the global semiconductor supply chain. The country is estimated to cover around 13 percent of global backend manufacturing.
According to official figures, in recent years the state of Penang has generated more than five percent of worldwide semiconductor revenue.
“The new test centre in Penang brings our manufacturing network closer to the companies that serve the further value chain of semiconductor manufacturing as well as to customers in this important Asian market. That shortens delivery times and routes, and it improves our competitiveness,” Bosch Board of Management Member and Chairman of the Mobility Business Sector, Dr Markus Heyn, said.
The frontend is where the actual circuits are attached and patterned on the wafers; at Bosch, for example, this work is currently performed in the clean rooms of the wafer fabs in Reutlingen and Dresden. The backend is where the individual chips are then separated from the wafers, assembled, and tested.
Bosch currently carries out most of the final testing of its semiconductors in Reutlingen, Germany; Suzhou, China; and Hatvan, Hungary. Those locations will now be joined by the new test centre in Penang, Malaysia.
The fully connected plant is one of the most advanced semiconductor test centers in Southeast Asia. Here, Bosch will immediately begin testing semiconductors that the company manufactures at its frontend in Dresden, among other locations.
“Our new test centre in Penang completes our internal process chain, especially for semiconductors from Dresden,” Dr Heyn said.
Bosch is pursuing a global growth strategy with its semiconductor business. Over the next three years, the company plans to invest some three billion euros in Dresden and Reutlingen, both as part of its own investment plan and under the auspices of the European IPCEI ME/CT (“Important Project of Common European Interest on Microelectronics and Communication Technologies”) funding program.
Following its expected acquisition of part of the business of TSI Semiconductors, based in Roseville, California, which is expected before the end of the year, Bosch plans to invest roughly an additional 1.4 billion euros in retooling the fab to support the latest manufacturing processes for silicon carbide semiconductors.
For more from Bosch, visit www.bosch.com.au