HDI’S INNOVATIVE INTERCOOLER DESIGN
HDi says the design combines efficiency, durability, and performance
HDi says the design combines efficiency, durability, and performance
Since its inception in 1996, HDi says it has solidified its position as a leader in intercooler design.
Its first 600x300x76 GT intercooler reportedly became the aftermarket standard for universal intercoolers.
The company says its dedication to meeting specific requirements has enabled it to go on to create what it describes as “some of the best heat exchangers available today.”
This article delves into the key features of HDi’s intercoolers and the extensive research and development process that has gone into producing these high-quality products.
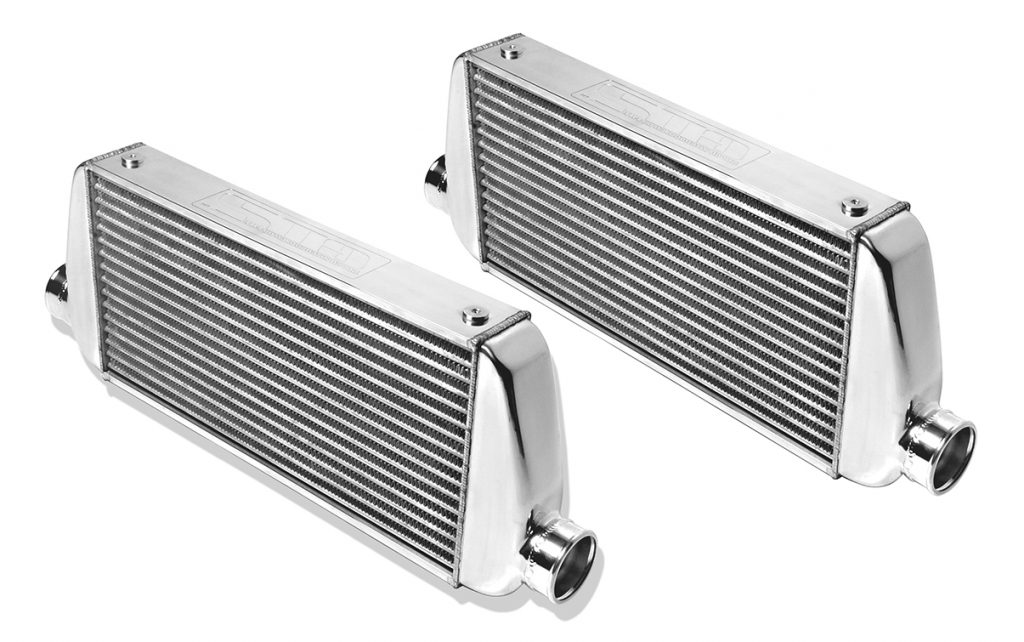
One primary requirement for any intercooler design is lightweight construction.
Heavy mass may seem a good heat sink, but it can also retain more heat energy and take longer to cool down, especially in situations where continuous high-speed ambient air streams are not readily available to remove retained heat.
The intercooler is not a heat sink, it is a heat exchanger, states HDi, which explains that it designs its intercoolers to be as light as possible, without sacrificing efficiency.
Further, HDi explains that keeping things light weight also helps to minimise the effect on change of weight distribution, especially when mounted far at the front of the car.
Another essential requirement is high efficiency.
To achieve this, HDi says it is vital to maximise the surface area for optimal heat exchange efficiency.
HDi reportedly accomplishes this through special features, such as high fin density and cross fin design.
It says the maximum contact surface area within the HDi GT2 intercooler core allows hot air energy to transfer through conduction heat to the outside surface and then dissipate it into the ambient air, resulting in high efficiency and superior cooling performance.
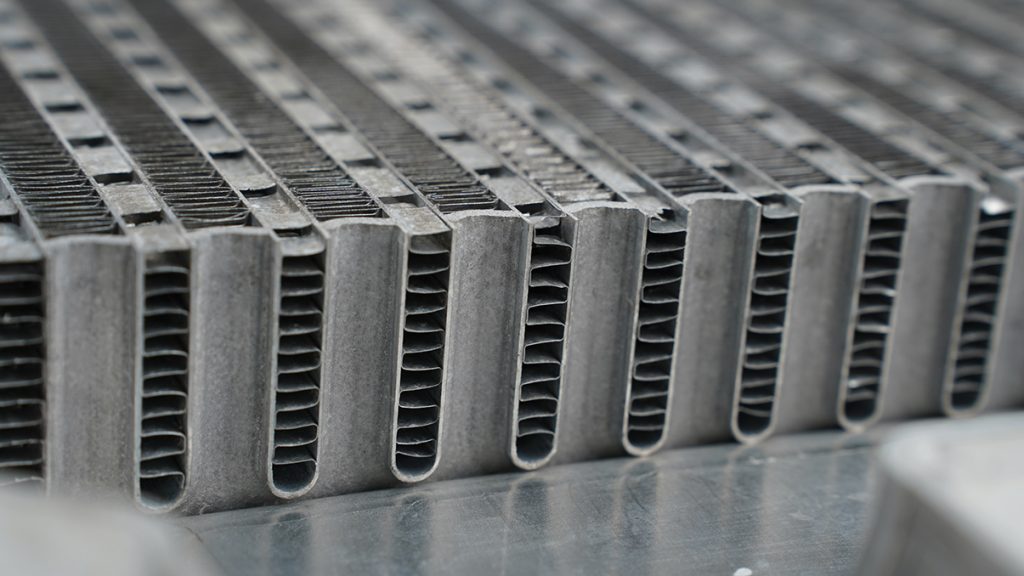
High flow is also crucial for an effective intercooler design, which HDi says it achieves through its innovative side tank shape design.
These tanks are formed from one high-quality aluminum sheet, instead of multiple sheets welded together or sand casted, which it says is a more advanced method which minimises cracking or leaking due to material fatigue from recurring heat and pressure cycles.
HDi states that this design is not only more affordable for consumers than using Billet CNCed tanks but is also critical in minimising pressure drop and creating the best possible internal shape for feeding the HDi GT2 high-efficiency tube and fin core.
It says the GTRS2 PRO intercooler port is also meticulously designed with award-winning and patent registered FHDi Clamps to match the tank’s outlet shape to further minimise turbulence.
Surface finishing plays a significant role in HDi’s design as well.
The HDi GT2 tanks and core are kept in their original finish, professionally manufactured to work as art, shining to reflect external radiation heat.
No painting or powder coating is needed to cover imperfections, which can act as insulation against heat dissipation.
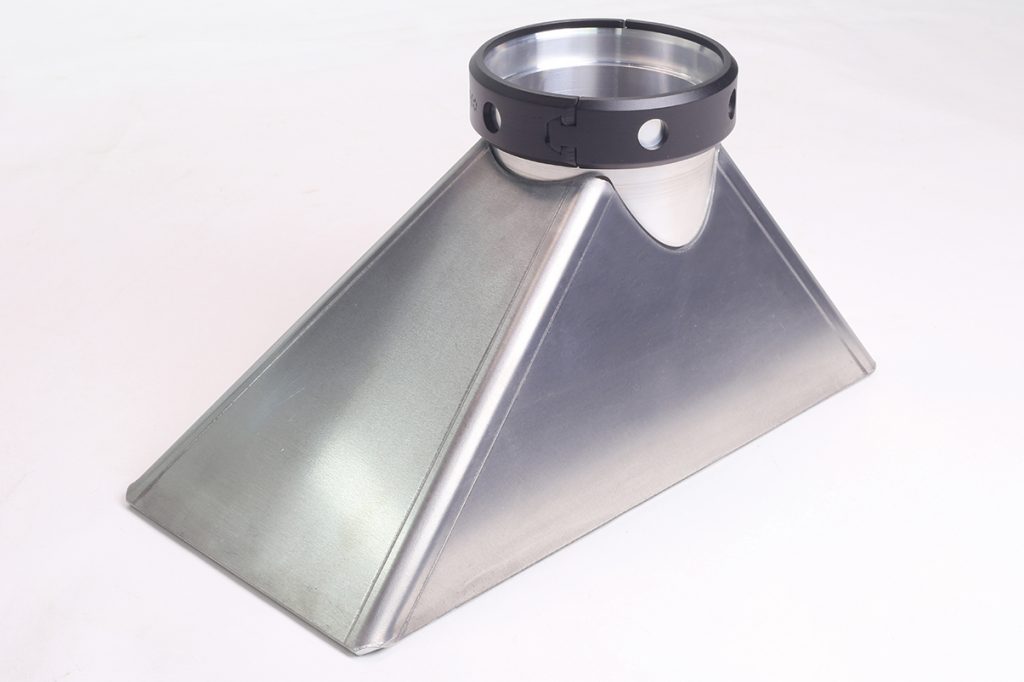
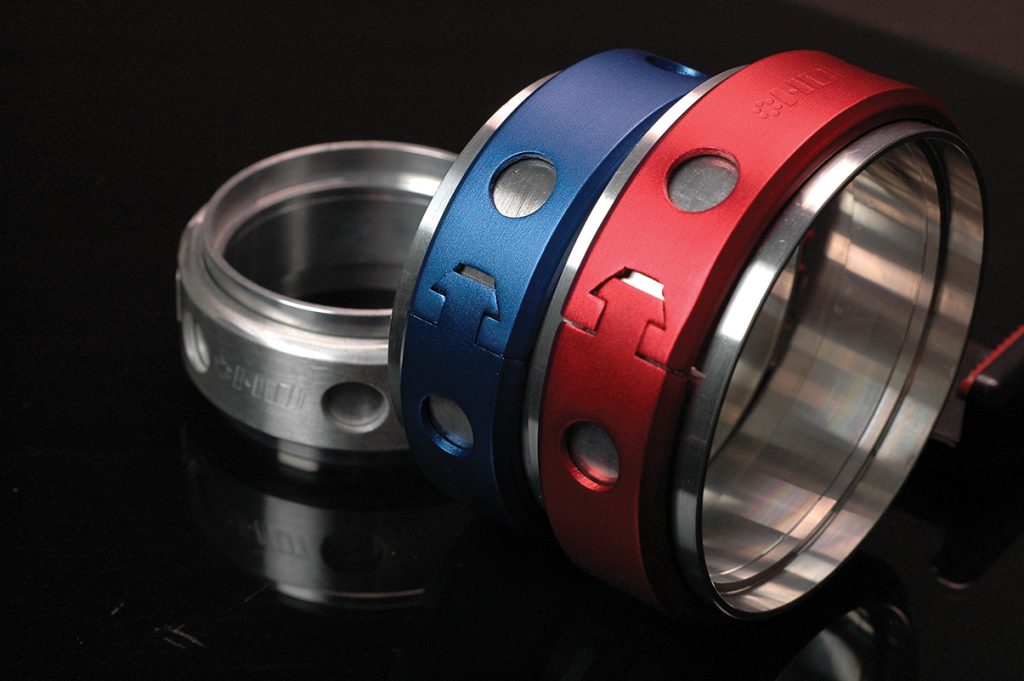
To develop an intercooler with superior cooling efficiency and minimal throttle response time, HDi must meet all these requirements while ensuring durability.
The ultimate goal is to enhance engine efficiency without compromising throttle response, increasing fuel consumption, obstructing the radiator, or affecting other engine heat dissipation components.
HDi says its comprehensive R&D process includes 3D scanning technology to digitise the OEM intercooler and its location, analysing the area for optimal size and route design.
All digital data is then converted into a CAD file ready for design.
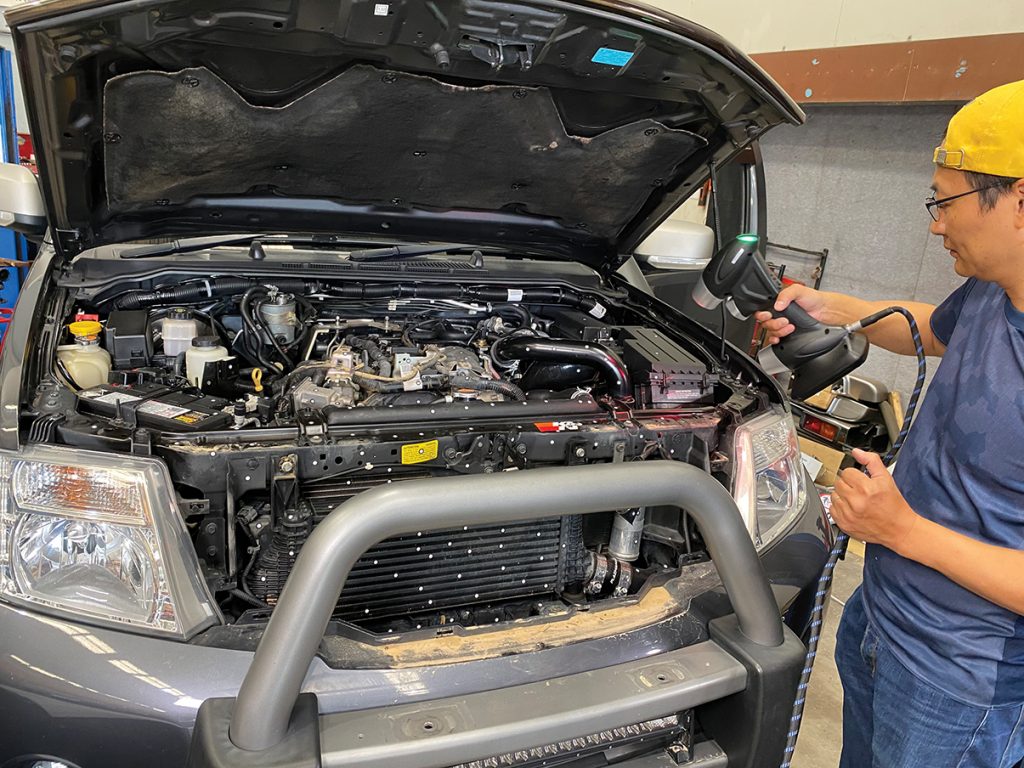
Fluid dynamic principles and HDi’s design principles are then applied to develop the best solution possible – including the shortest route, minimal restriction, highest flow, maximum cooling efficiency, and lightest weight.
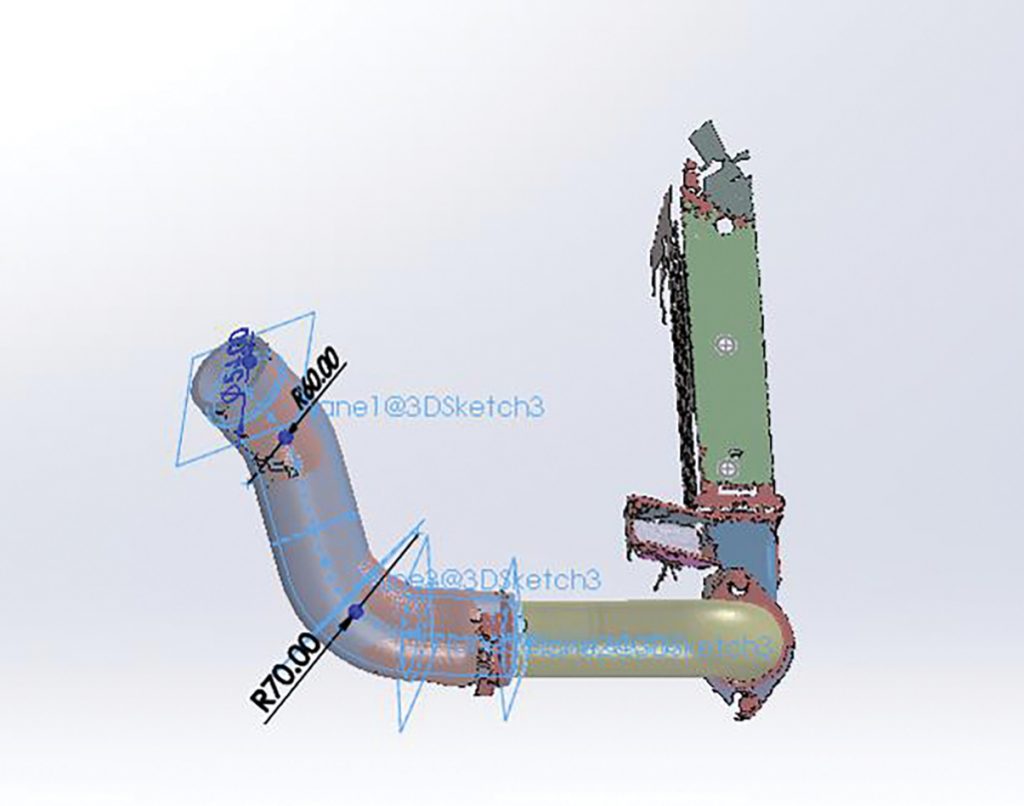
Once the design is confirmed, it undergoes various performance computer analytics and simulations such as flow rate, pressure drop, high heat and pressure spots before prototyping.
Depending on the application, prototypes may involve 3D printing or CNC machining.
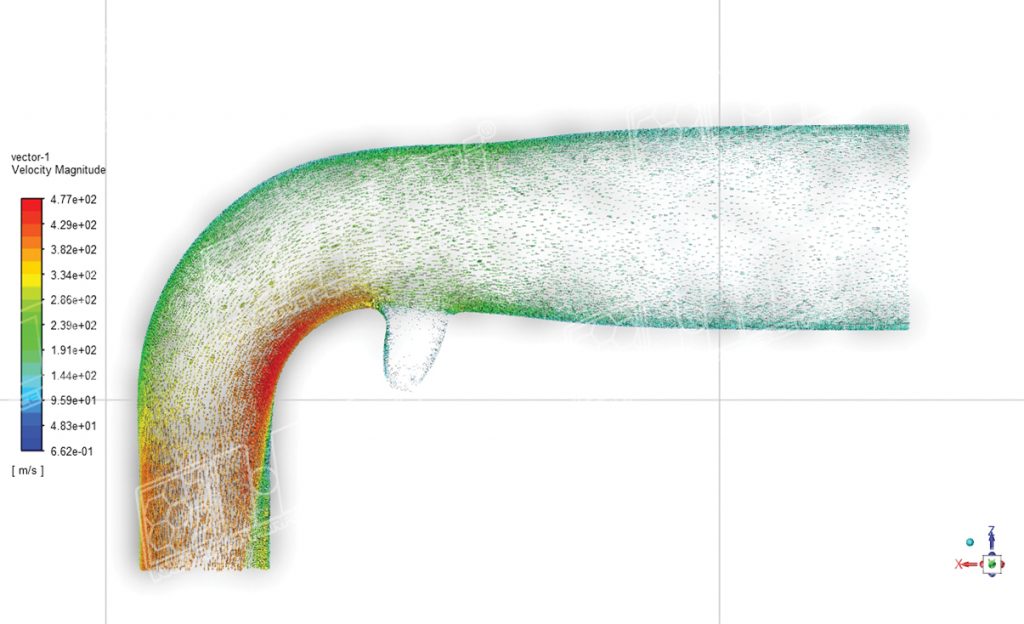
The kit will then be ready for trial fitment with dyno and road tests conducted to confirm the design’s efficiency before mass production commences.
In addition to these innovative design principles, HDi says its R&D process ensures its intercoolers are “of the highest quality, delivering superior performance and durability to customers.”
It states the HDi GT2 intercooler is an excellent example of the company’s innovation in intercooler design.
HDi explains the GT2 intercooler is a simple replacement for the OEM intercooler, with many kits being direct bolt-on, making installation “a breeze”.
The high fin density and cross fin design maximise surface area and allow for optimal heat exchange efficiency.
The side tank shape design ensures high flow and minimal pressure drop, providing the best possible internal shape for feeding the high-efficiency tube and fin core.
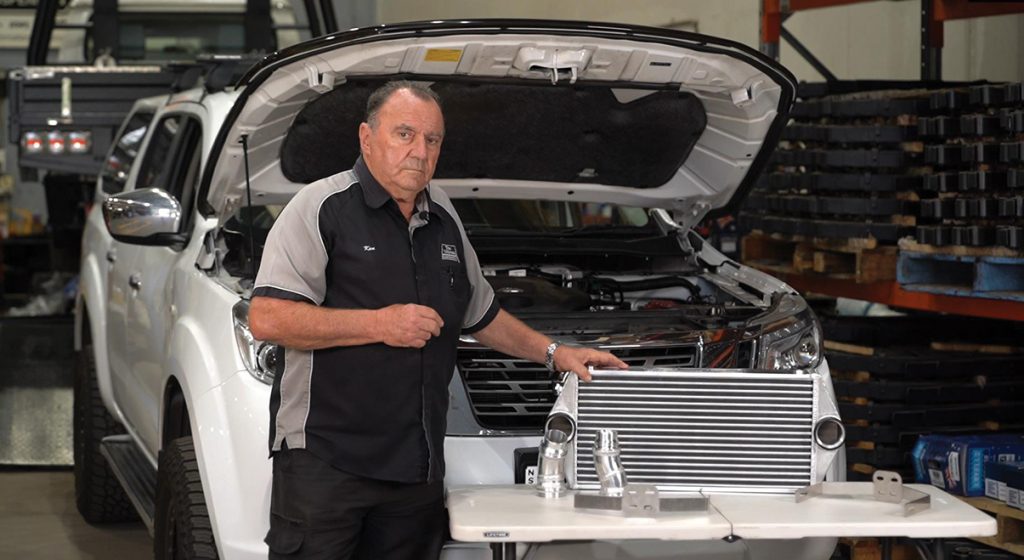
In addition to its excellent cooling performance, the HDi GT2 intercooler also looks great under the hood.
The tanks and core are kept in their original finish, professionally manufactured to reflect external radiation heat, making them shine like a piece of art.
Overall, HDi’s intercooler design principles and R&D process ensures that its intercoolers are of the highest quality, delivering superior performance, durability, and efficiency.
HDi products are available from Australian Ultimate Suspension, with Managing Director, Ken O’Keefe, reporting that his company is working with the HDi team in order to develop more performance intercoolers.
“If you are interested in becoming a dealer, please do not hesitate to contact us,” Ken said.
For more information, visit www.ultimatesuspension.com.au
Dealer enquiries are welcome