CHOOSING THE RIGHT ROTOR FOR THE TRACK
DBA says it is manifesting its position as the Australian ‘go-to’ brand for motorsport and car enthusiasts
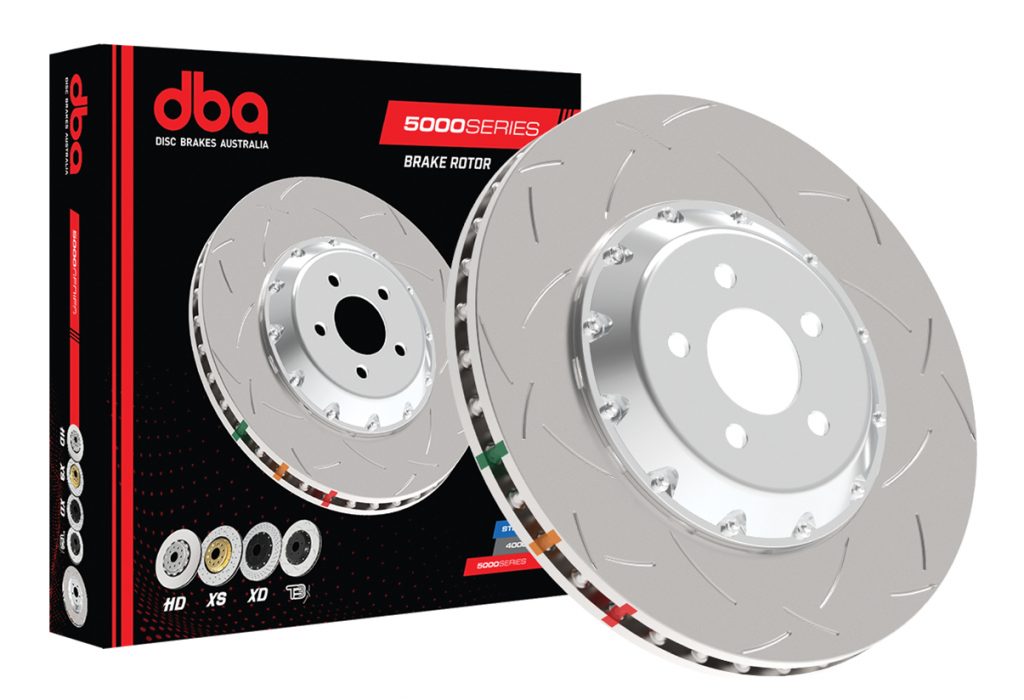
Offering invaluable advice through its Australian Customer Support Teams is only one of the many ways Disc Brakes Australia (DBA) says it can help you to get track ready.
Choosing the correct brake setup for a successful day at the track can often be confusing and expensive, if you use a product not fit for purpose.
The aftermarket industry is very competitive and full of sales hype to attract buyers. However, aesthetics or ‘bling’ are no substitute for product performance when attending a track day and partaking in any form of motorsport competition, warns DBA.
DBA has been manufacturing brake rotors for more than 45 years in Sydney, Australia. Throughout that time, it has held strong connections with Motorsport both at grassroots and professional levels.
This commitment has resulted in countless hours of product testing through situations of extreme demand, including rally, endurance, and various other racing codes. Constantly testing the limitations of its rotors has resulted in continuous advancements in product performance and durability.
“We’ve recently announced a significant partnership with Motorsport Australia, thus demonstrating our commitment to the Australian motorsport community and the Australian market,” DBA General Manager, Phillip Joseph, said.
“This collaboration will allow us to work even more closely with motorsport teams across various categories and will enable us to continuously enhance our braking expertise and competence.
“Being an Australian business with our own R&D, manufacturing and distribution puts us in the unique position of being extremely close to the action.
“Our Product, R&D and Sales teams benefit greatly from liaising directly with the market, be it at motorsport or car club events interacting with race teams and car enthusiasts alike or talking directly to our distributors and workshop customers.”
Temperature management
The two most important factors when it comes to brake rotors used in extreme applications are heat capacity and thermal stress management.
Heat capacity design is a compromise between having sufficient metal mass in the friction ring to accept and process the kinetic energy transferred into the brake system to decelerate the vehicle, and trying to minimise the rotating mass of the wheel assembly (unsprung weight).
DBA explains that its 4000 and 5000 Series upgrade performance rotors address both these issues. The formula of XG-150 cast iron in combination with the patented ‘Kangaroo Paw’ internal pillar and post vent design offers optimal temperature properties, whilst the 5000 Series two-piece rotors minimise the unsprung weight by using ultra lightweight aluminium hats.
Thermal stress management is about minimising fatigue to prolong the life of the rotor. Regardless of the manufacturer or rotor design, grey cast iron will fatigue in motorsport applications. The thermal expansion from heating and contraction when cooling initiates a stress and strain cycle, which is essentially metal fatigue.
It is therefore recommended and best practice by professional race teams to regularly inspect rotors after every session and discard them after a known period depending on conditions and application to avoid any unpredicted failures due to metal fatigue. Again, DBA upgrade performance rotors prolong the rotor’s safe use period by using one of the most advanced metallurgic compositions available.
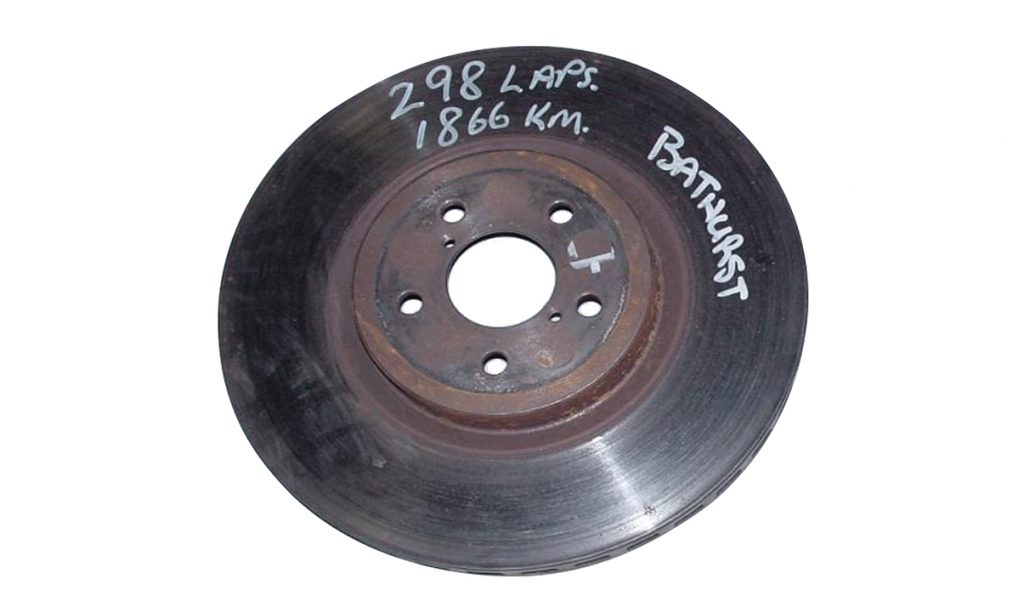
Surface design
DBA says that without question, when it comes to track and racing applications, it is slotted rotors wherever possible.
There are drivers that like to maintain the factory setup with plain face rotors, and this is okay. Certainly the rotor pictured above was a plain type due to the racing class requirements it was entered in.
The purpose of slots in the brake rotor is to evacuate the waste material (dust) from the friction surfaces.
The slots will ensure consistent friction performance throughout the life of the brake rotor and pad, whereas more scrutiny is required in friction material selection with plain surfaces to avoid surface glazing and declining friction performance. This leaves us with drilled or drilled and slotted.
Drilled brake rotors are not recommended for track use of any kind, as the drill holes are focus points where stress and fatigue will accelerate and eventually result in crack formation.
Drilled rotors have proven to improve braking performance on the street where normal driving conditions rarely exceed 250oC and stress is not a concern, however in motorsport applications drilled rotors are to be avoided.
DBA says this is where its 4000 and 5000 Series rotors come in, stating that with their patented T3 slots, they offer the perfect design for race and track applications.
Thermal stability
There are several treatments or processes applied to brake rotors marketed in the industry to achieve thermal stability, but not all of them lead to the same outcome.
DBA explains that its 4000 and 5000 Series rotors undergo prolonged heat cycles under strictly controlled conditions, known as Thermal Stability Profiling (TSP), to relieve any internal stresses sustained from the manufacturing processes.
It says this ensures maximum thermal stability and reduced metal fatigue in extremely high demanding applications.
“While there are many options available in the market to motorsport teams and enthusiasts alike, trusting DBA with its nearly 50 years of local development and manufacturing experience gives you the peace of mind, when performance really matters,” Phillip said.
For more information, contact DBA’s Customer Support Team on 1800 730 039 or visit www.dba.com.au/contact